Tooling & Injection Molding Capabilities Under One Roof
Six Benefits You Should Keep in Mind
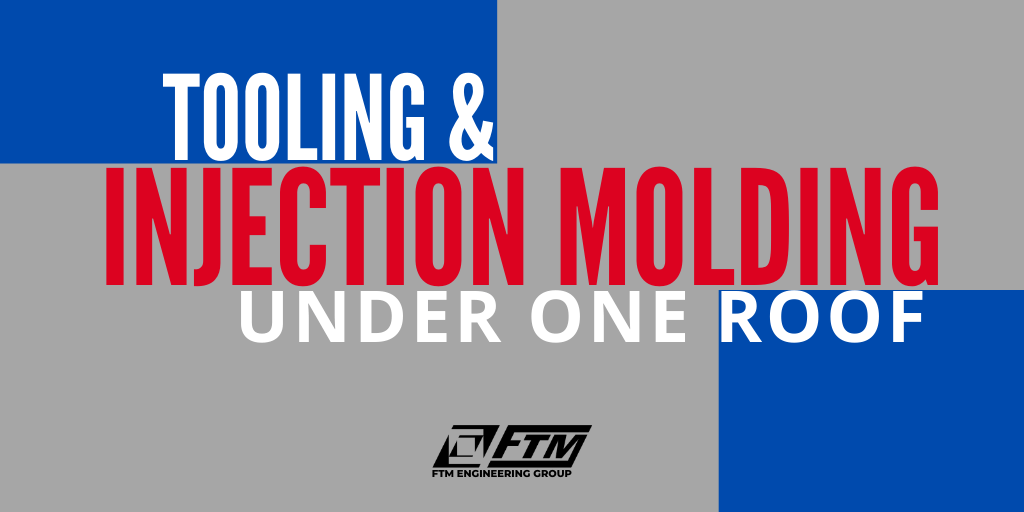
Tooling & Injection Molding Capabilities Under One Roof: Six Benefits You Should Keep in Mind
When most people think of plastic injection molded parts, they consider the “tool” and the “part” two separate things - two different processes, two separate companies usually. That is typically how it’s been done for years. More innovative businesses, however, are now able to offer both capabilities under one roof, and there are several benefits to this concept.
FTM Engineering Group combines a best-in-class injection molding department and a truly world-class tool engineering department under one roof. Working with FTM Engineering Group’s team of professionals offers you peace of mind that’s hard to find. We may not have coined the phrase One Stop Shop, but we’ve certainly perfected it.
The Benefits of a One-Stop Shop
A one-stop-shop for both tooling and plastic injection molding is an idea that many have tried, but few have perfected. Building a tool for a plastic injection molded part and producing a part involve two wildly different skill sets and experience. But, when done properly, the benefits are hard to miss.
Lead Time: Time is lost when a mold is sourced to an outside vendor and the molding department has a machine waiting for that vendor to deliver the mold. At FTM Engineering, the mold is just steps from the molding department. We’re talking minutes and hours, not days or weeks when it’s time to get your mold in a press.
Tool Maintenance: Whether for routine maintenance or an unforeseen event, our tool maintenance department prioritizes routine inspections of cavity and core detail, waterlines, parting line integrity, ejector systems, leader pin alignment, and hot runner and manifold systems. We start work on your mold ASAP after the last shot has been retained.
Uptime: During a recent customer visit, there was discussion about a minor engineering change to the mold running production. We reviewed the change, got the green light on the spot, the steel change was made, and the mold was back in the press the same day. Ask your injection mold vendor if they can do that!
Communication: Our quality, engineering, and manufacturing teams meet regularly to ensure that we are engaged collaboratively with our clients. Transparency in everything we do is just good business.
Synchronized Scheduling: For more than 40 years, process alignment has meant a seamless transition from the tool shop to the molding department. During your next visit to FTM Engineering, we’ll show you the benefits that come from our synchronized scheduling approach.
QMS: Our ISO 9001-2015 Quality Management System (QMS) touches every process at FTM Engineering Group. Integrated and synchronized molding and tooling teams monitor and document each step. We are intentional and driven to satisfy our business partners.
Consider these benefits for your next project.
Have you run into issues in the past dealing with multiple vendors for tooling and plastic injection molding production? Check us out. See how a one-stop shop could help improve your productivity, decrease costs and time, and increase the quality of your parts.
Let's start by scheduling a quick call. Contact us today or go ahead and request a quote.