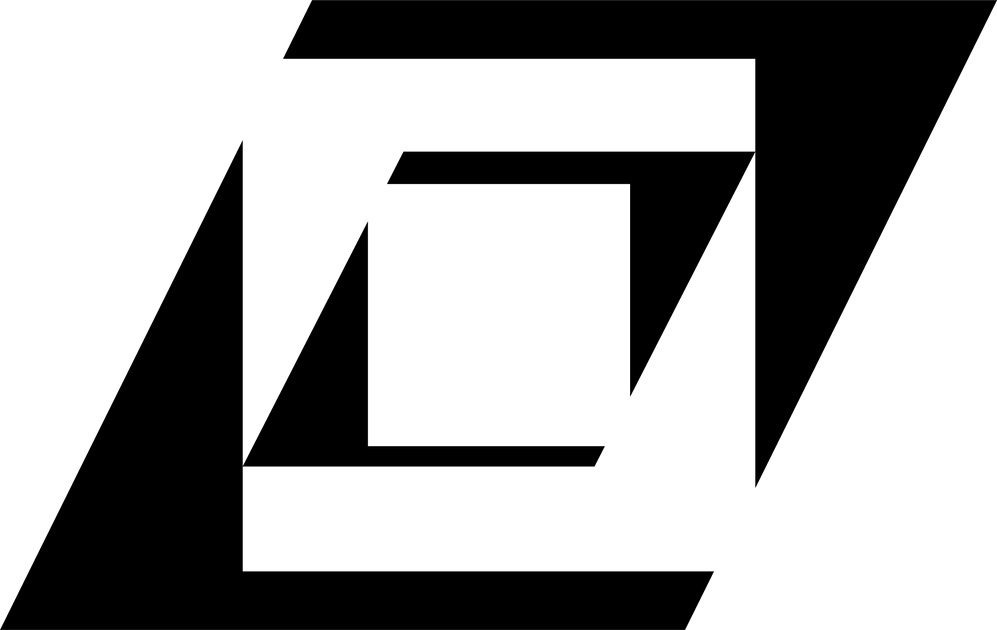
Success Stories
Precision Tooling & Injection Molding Success Stories
To provide the best service to our customers, we specialize in the design, engineering and production of the precision fabrication of injection molded products and tooling. We provide these services for customers in a wide range of industries. Here are just a few examples of the quality products and value added services that we deliver every day.
Wondering if we’ll be a good fit for your next project?
Learn more about us and discover whether or not we’re the right partner for you.
Success Stories - Automotive
Precision Mold Manufacturing for a PPS Housing for the Automotive Industry
(The product shown here was manufactured with molds designed and fabricated by FTM Engineering. See Custom Tooling.)
This product highlights our ability to manufacture complex, precision designs for a wide array of applications. Designed to be used in an automotive application as a transmission component, the mold fabrication included various machining techniques to achieve the precision required.
This mold was machined utilizing our Mitsubishi FA Wire EDM and Charmille Roboform EDM. Our precision machining was completed on an OKK CNC machining center (for graphite). The finished molded component featured dimensions of 4.065" in length, 3.745" in width, and was 1.605" in height. Tolerances included ±0.05mm, a true position of .1mm, parallelism of .1mm, and flatness of .1mm. The finished component would also require material finishes of #32 covered grain. This finish is applied to all surfaces except the hatched area, which has #45 cover applied. The finished mold was then shipped to the customer in Lyon, France for inspection and testing.
Success Stories - Electronic Components
Precision Tooling for an Injection Molded Pin Connector Housing for the Electronic Component Industry
(The tool shown here was fabricated for the injection molding of a 36 pin circuit board protector.)
This tool was designed to the customers supplied prints, and featured interchangeable components that would allow for the injection molding of four individual parts. The complexity and precision required for this mold utilized a number of our CNC machining and hard milling capabilities.
Fabrication entailed graphite milling, which was completed on our OKK machining centers, as well as wire and conventional EDM machining, done on a Mitsubishi wire EDM and a Charmilles Roboform sinker EDM.
The molded component would be molded from a 20% GF PBT Ultradur B 4300 G4 natural resin, with a green colorant.
It featured dimensions of 82.2mm in length (+.0/-.2"), 27.4mm in width, and 24.5mm in height (±.2mm), with a finish of RA 2.24 or smaller.
To verify the integrity and quality of the tool, initial part sampling and debugging was performed in-house prior to shipping to the customer in Myrtle Beach, South Carolina. The entire project, from design to delivery, was completed in just 10 weeks.
Success Stories - Heavy Equipment Industry
Multi-Cavity Auto Unscrewing Plastic Injection Mold for the Heavy Equipment / OEM Industry
This high quality injection mold is just one example of FTM Engineering’s ability to handle the most complex challenges. This four-cavity mold was designed with a hot runner system and utilizes floating cores, mechanical and spring loaded slides, hydraulic motors and a gear box built in to the design. Total design completion and acceptance in 3 weeks.
New Tooling – FTM Engineering design capabilities bring to our customers the most cost effective tool designs resulting in high quality, low maintenance tooling. We are able to maintain short lead times and respond to the most demanding timelines.
Engineering Changes – Designing new features into existing tooling requires innovation and creativity: FTM Engineering excels in creating cost effective solutions to the most challenging proposals.
Solve Design Issues on Existing Tooling – Evaluating and identifying design shortcomings are essential to the success of solving chronic sub-standard tooling issues.
5 Ways to Reduce Lead Time for Your Precision Parts
(And still get a quality product!)
You’ll win the day when you download this free guide and show your boss how you’re not just focused on developing a great product, but also concerned about the bottom line.
Success Stories - Consumer Industry
Engineering of a Hand Pump Mold for the Consumer Industry
FTM Engineering Group worked together with the customer’s development team on concept and product configurations, then designed nine (9) prototype plastic injection molds producing hand pump assemblies for the consumables industry. Upon approval of engineering concepts and feasibility, FTM Engineering Group designed all nine prototype tools in four weeks. The prototype molds were manufactured by Faith Tool & Manufacturing.
FTM Engineering is poised to design, build, and produce prototype parts in as little as 5 working days dependent on the part complexity.
During the tool concept and development phase, our tooling engineers will anticipate production conditions and make recommendations to improve part function and durability. Our Engineers will work directly with your Product Engineers to develop parts that are functionally sound and moldable. Having a clear understanding of part function is critical in determining appropriate tooling requirements.
FTM Engineering Group will make recommendations for new parts, molding processes, & tooling specification. Our capabilities include evaluation and analysis of part geometry and the skill to pinpoint problem areas that can hinder the tooling and molding process. This allows us to reduce tooling and molding costs by producing functional low maintenance tooling. Effective tooling translates into optimum molding conditions.
Mold flow analysis – establish molding processes and improving existing conditions. Our mold flow analysis gives us the ability to anticipate potential processing obstacles which can hinder cycle times and part quality. Our Process Engineers are fully trained specialists in the scientific molding process and are able to diagnose symptoms and recognize cause.
Success Stories
Resources
Established in 1976. © 2025 FTM Engineering Group Corp. All rights reserved. Privacy Policy | Sitemap